Master a number of independent research and development core technologies, and is committed to the corrugated packaging industry towards the whole plant intelligence
- The Dry-end Control System
- The Dry-end Control System, equipped with independently patented high-precision motion control technology and multi-axis synchronous control technology, enables centralized control of the entire production process. It ensures high precision and stability, enabling high-speed synchronization in line production. This system allows you to effortlessly handle the frequent changing of production orders and manage various types of orders.
- The wet end control center
- The wet end control center is capable of distributing data from the material formulation database and order changes from the production management system to the double facer and single facer systems. It intelligently recognizes environmental humidity, raw paper moisture, material characteristics, speed, and adhesive properties to ensure the quality of corrugated formation.
- Crosscutting system
-
Highest speed 400m/min
Accuracy ±1 mm
500mm production speed 220m/min
- Multi functional cutter control system
- During the automatic order change process, the production management system issues a command to the cutting machine to automatically cut off the material.Depending on the requirements of different orders, it automatically selects between full-width cutting, edge cutting, or center cutting modes. The highest cutting speed is 300 m/min The cutting precision is 0.5mm.
- Temperature Control
- Adjusting the temperature levels based on temperature sensors, material properties, and speed variations through the Wet End Control Center.
- Single Facer Bridge
- Bridge paper feeding control, dual system control with inkjet detection and infrared measurement,bridge deviation correction system control.
- Preheating Cylinder automatically
- Adjusts the comer radius based on the material
- Single Facer
- Retrieve data from the process recipe database and adaptively adjust pressure, temperature,adhesive amount, comer radius, etc.
- Stacker control system
-
The overall brush automatic control system is regulated by the cutting length, cardboard thickness, and brush pressure ratio network to achieve neat paper output The front and rear baffles are bi-directionally linked to precisely and reliably change the order in batches.
It allows for stacking multiple orders, staggered stacking, and mixed stacking. The speed is 9 seconds faster compared to traditional methods.
- Waste discharge system
- Highest waste discharge speed 400m/min
Without decreasing speed 300m/min
- Slitter control system
-
Highest speed 400m/min
Accuracy: 0.5mm
Maintain speed while order change:300m/min
Order change waste: within 500mm
- Pressure Plate Control
- Automatically adjusting the pressure plate through the Wet End Control Center.
- Starch Block Plate
- Automatically controlling the width of the starch block plate through the Wet End Control Center.
- Glue Amount Control
- Adjusting the glue amount gap based on material and speed variations through the Wet End Control Center.
- Paper feeder + Paper rack
- One-click automatic paper feeding, paper unloading, and automatic alignment
- Paper rack control
- Automatically feeding and aligning the parent paper roll through the Wet End Control Center.
- 01 CD high-speed bus technology
- 02 High-precision motion control algorithms
- 03 Multi-axis synchronous control technology
- 04 corrugated line control technology
- 05 The carbon fiber knife cylinder production technology
- 06 Laser velocity measurement technology
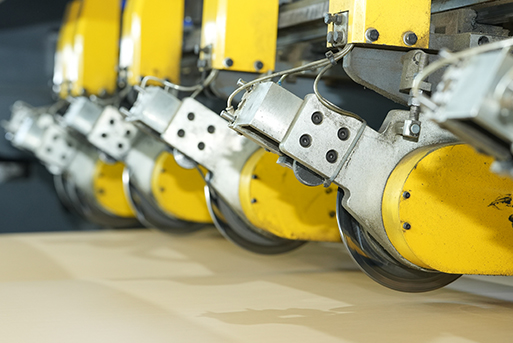
In the technical framework of the industrial Internet, the workshop site needs to access different equipment, systems and products through various communication methods, and realize the collection and upload of massive data.
The company's production management system and wet-end control center use PROFINET bus for data acquisition and storage; The stacker, longitudinal machine, and cross-cutting machine are controlled by EtherCAT, CANOPEN, and EtherNET/IP industrial buses for multi-axis synchronous control.
The application of high-speed bus technology ensures the real-time and security of data collection, and improves the effectiveness of fast and accurate control of intelligent devices and massive data access.
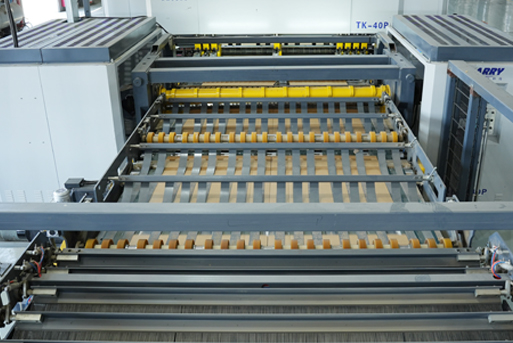
High-precision motion control technology is the core technology of intelligent corrugated cardboard production equipment. For a long time, this technology has been mainly mastered by foreign companies. After years of technology research and development, the company has formed a relatively complete high-precision motion control technology, which has enhanced the company's core competitiveness.
The company has independently developed the speed algorithm of five motion curves and S-type acceleration and deceleration control, and applied for an invention patent. The five-order curve can ensure the continuous angle, angular velocity, angular acceleration and angular jerk of the machine, reduce the impact of the machine, and the position movement is smoother and smoother. The algorithm effectively solves the wear and tear of high-speed and long-term movement of machinery, prolongs the service life of machinery, makes the equipment more stable, and reduces the failure rate.
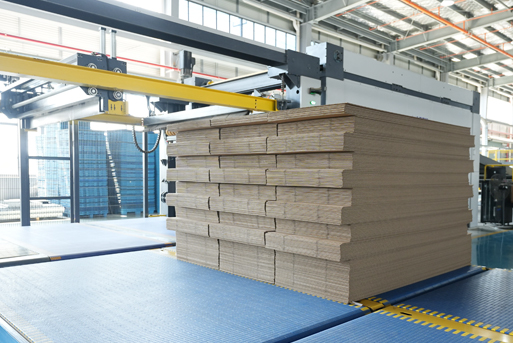
Multi-axis synchronous control technology is an interdisciplinary and comprehensive technology that integrates power electronics technology, electrical drive technology, information technology, control technology and mechanical technology. The company has developed a dual-drive, four-wheel drive and multi-drive servo synchronous control system, which is a coordinate motion instruction, which can drive two and more motors to run at the same time, and through the detection of the motor movement, the displacement deviation is fed back to the CNC system to obtain synchronous error compensation.
In the multi-axis synchronous control, the company's master station adopts position and speed control accuracy, and the speed limiting and torque control are used from station B, combined with speed limiting, multi-axis synchronization is better, the accuracy is higher, and the occurrence of flying phenomenon can be avoided when the slave station fails, which can effectively reduce the loss of machinery.
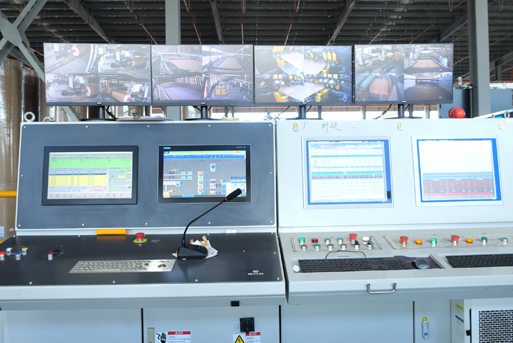
The company's self-developed corrugated cardboard production line control technology includes a dry control center and a wet end control center, which can be seamlessly connected with the dry and wet end of corrugated cardboard production through bus control;
Realize the automatic production, speed synchronization and adaptive cruise of cadre equipment, so that the cadre equipment can achieve full integration, systematic control, data-based intelligent management, report analysis, paper splicing statistics, logistics packaging efficiency statistics, automatic waste cutting and discharging, multi-terminal remote monitoring, and automatic fault call;
The wet-end control center can complete the data distribution from the wet-end control center to the double-sided machine and single-sided machine system according to the order change of the material formula database and the production management system, and intelligently identify the characteristics of environmental humidity, base paper humidity, material, speed and glue to ensure the quality of corrugated molding.
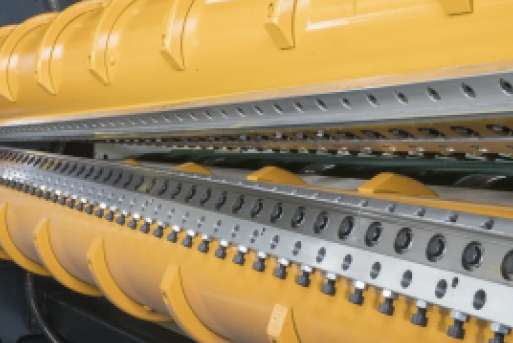
The cross-cutting machine with carbon fiber cartridge has the characteristics of ultra-high speed, high precision and strong stability.
Compared with similar products, Jiapeng's cross-cutting machine system can reach a maximum operating speed of 400m/min, and 220m/min under 500mm fixed length, which has unique advantages and advancement in small-size orders, and has obvious advantages over the current speed of about 150m/min in the industry.
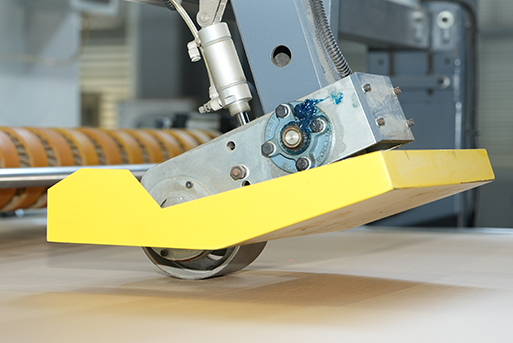
The company has developed a laser velocity measurement technology using laser technology to measure the feeding speed of corrugated paper.
This method avoids slipping and contact, and the correspondence between the cutting rate of the cutter and the movement rate of the corrugated paper is obtained according to the speed following controller, which can ensure the accuracy of flying cutting while reducing the error.
In addition, by detecting the error of laser velocity measurement and correcting the measurement distance, the accuracy and stability of laser velocity measurement can be effectively improved, and the flying shear error of the cross-cutting machine can be controlled in the range of less than 0.5mm, so that the cross-cutting machine can maintain accuracy at a high speed of 400m/min.